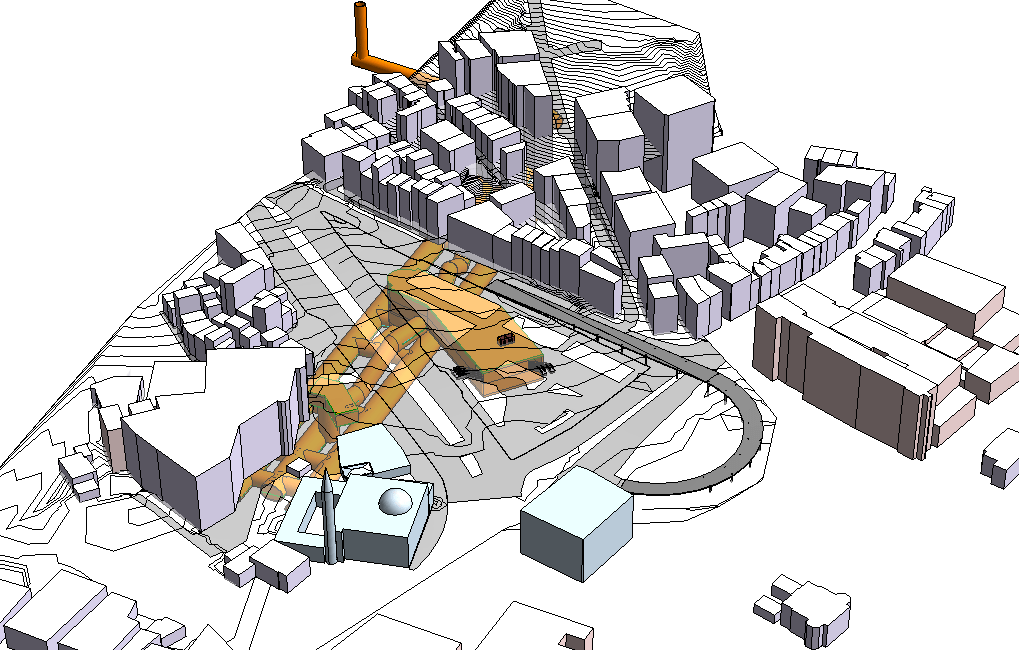
When it comes to control and keenly plan the manufacturing process details, a cost-effective software that comes handy is BIM. One can say that BIM is an enhanced version of the CAD. It is a software, or rather, a technology with which most of the engaging problems related to infrastructure development in planning, designing, building and managing can be solved into high productivity, cost-effectiveness and quality.
BIM’s model-centric approach provides an up-to-date and the shared understanding of the projects to all the stakeholders. Since BIM can simulate almost all aspects of a project from the beginning to the end, it is finally entering the mainstream of infrastructure. BIM, for once, has changed the nature of designing, constructing and delivering an infrastructure project. It is one of the major tools of the present scenario, which can dig out all the possibilities of improvement in productivity, quality, cost, asset management and construction in the infrastructure field.
BIM is rising as a future for the old ways of working which are no more sufficient. Public, Private and government sectors are focused on BIM to moderate the lifecycle costs and deprecate the gaps in the funding to meet the dire infrastructure needs of the world. Certainly, BIM is a big relief for the infrastructure development sector.
BIM with DFMA
A factory controlled environment of producing infrastructure solutions instead of construction on-site, provided by DFMA, is the edge that brings multiple improvements, possibilities, less time-consuming and cost-effective to the infrastructure sector. DFMA clubbed with BIM unlocks limitless opportunities and great potential for the construction field.
Transferring and sharing the information is one crucial aspect to BIM and DFMA. It is vital to design with BIM to open more practical means of creating and maintaining assets. The most practical and cost-effective way to receive high rates of productivity on site is to adopt the offsite approach of DFMA and utilising the BIM technology together. With a closer approach to it, it becomes very clear that the disciplinary and collaborative approach that is provided and facilitated by BIM goes hand in hand with the needs of prefabrication for the early coordination and the 3D designing information that is required by DFMA for its offsite approach.
DFMA is the technology that concurrent engineering processes use to simplify and create the structures offsite to reduce the cost, labour and timing. It is safer to say that BIM utilised with DFMA is going to provide greater possibilities in the upcoming future.
About author
Ameer Muhammed at BIMARC which is a leading BIM Services and Architectural 3D Modeling Services provider to customers in the UK, US, Australia, Canada, Europe, India and the Middle East.